With the highest cut quality, minimum waste and low maintenance needs, our range of flying cut-off machines includes solutions for every tube size, material type, steel grade and performance requirement.
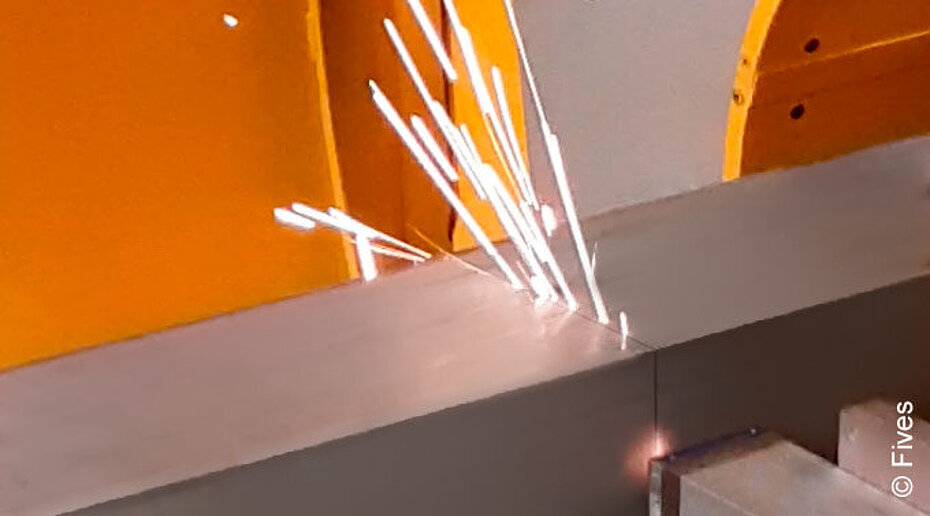
Cost-cutting
Our fiber laser cut-off technology, designed for stainless steel applications, reduces the operating cost by 80% compared to traditional orbital cut-off solutions. Speeds vary from 20 ¨C 50 m/min and is designed for stainless steel applications.
- No blade changes
- Zero changeover time
- No need for lubrication or cooling
- Simple maintenance with easy access from the top
FLYING COLD CUT-OFFS
Our flying cold saw cut-offs ensure the highest quality and safety with precise cuts and minimal tolerances. They are designed for easy maintenance and reducing downtime. The advanced technology prolongs blade life, saving on replacement costs and maintaining cutting performance over time.
A wide range of models:
- Single blade cold saw cut-off
- Twin blade cold saw cut-off
- Orbital cold saw cut-off
- Four blade milling cold saw cut-off
FRICTION SAW CUT-OFFS
Flexible and widely applicable technology for cutting hard materials as well as big tube sizes, all at high speeds. It ensures maximum operational safety and final product quality.
BLADELESS CUT-OFFS
Innovative bladeless technology for any material: laser cutting for stainless steel tubes and plasma cutting for carbon steel tubes. These provide fast, high quality cuts that significantly reduce mechanical stress, equipment wear and avoid blade use.
Advanced cut-off control
All models are equipped with a microprocessor that manages all unit functions, ensuring reliable and accurate cutting lengths, precision and minimal maintenance:
Cut-off MANAGER
The easy-to-use Cut-off Manager system allows the operator to simply set all key cutting parameters, and automatically provides feedback and statistical data. The result is an optimized cutting sequence with increased cutting speed, reduced scrap, and lower machine wear.
Blade manager
The Blade Manager software collects data on the blades used and their original supplier. Every cut, incidence and square meter of cut material is stored in the database, supplying the information needed to choose the optimum blade for each application.